Sea ports are easily vulnerable to safety hazards. With a huge number of heavy vehicular movements, different dimensions and types of cargo being loaded, unloaded and moved within port premises it becomes very important to be alert when walking, driving and moving around in the port premises during all times of the day and night since the chances of trips and falls increases. Furthermore, people working with cargo at ports face safety risks every day due to - working at heights, falling cargo, heavy machinery, traffic and other hazards. Factors like untrained and casual labor, complacency in handling cargo, long hours or inadequate breaks further increase the risk of injuries and accidents. To mitigate any risk of injuries or fatalities a general awareness of the operations cannot be undermined and a detailed risk analysis and adoption of detailed safety protocol is essential.
Generic safety norms expected from a port user like donning of Personal Protective Equipment (PPEs) in cargo handling areas, compliance of set safety rules or norms, no misuse of any equipment, deployment of only trained personnel in the docks are insufficient and a more holistic view is necessary to not only identify the risks, but include specific measures to eliminate those risks in a structured manner.
To enhance the safety culture at J M Baxi & Co, a more structured approach on all the risks involved in seaport operations are identified, and bought under the ambit of Six Guiding Stars of Safety. Every J M Baxi employee is to not only adhere to these but also inculcate them in their daily working lives, which are.
- Safety whilst moving
- Safety aboard a vessel
- Mobile equipment safety
- Cargo handling safety
- Safety when working at a height
- Lifting equipment safely
All the anticipated risks are identified and risk mitigation methods are placed which becomes the standard procedure for work under that Guiding Star.
The Guiding Star no. (i) to (iii) are generally for all the port users and (iv) to (vi) are specifically for people involved with cargo operations in a port.
Here is a detailed look at the Guiding Stars
I. Safety whilst moving
Activities under this principle are to identify tasks which may jeopardise safety whilst walking, moving around in a vessel/seaport area and bringing n measures to eliminate the risk. For effective compliance with this standard:
A. The supervisor and employee should identify and control the risks associated with the presence of moving equipment and pedestrians, to ensure.
- Interaction between pedestrians and moving equipment is eliminated
- Consistent use of high visibility clothing
- Effective communication between pedestrians, operators of moving equipment and those supervising operations of the moving equipment
B. The employee shall walk only on the pedestrian path in the designated areas on the vessel/ port
C. Wearing PPE i.e. - high visibility vest, safety helmet and safety shoes when moving within the port
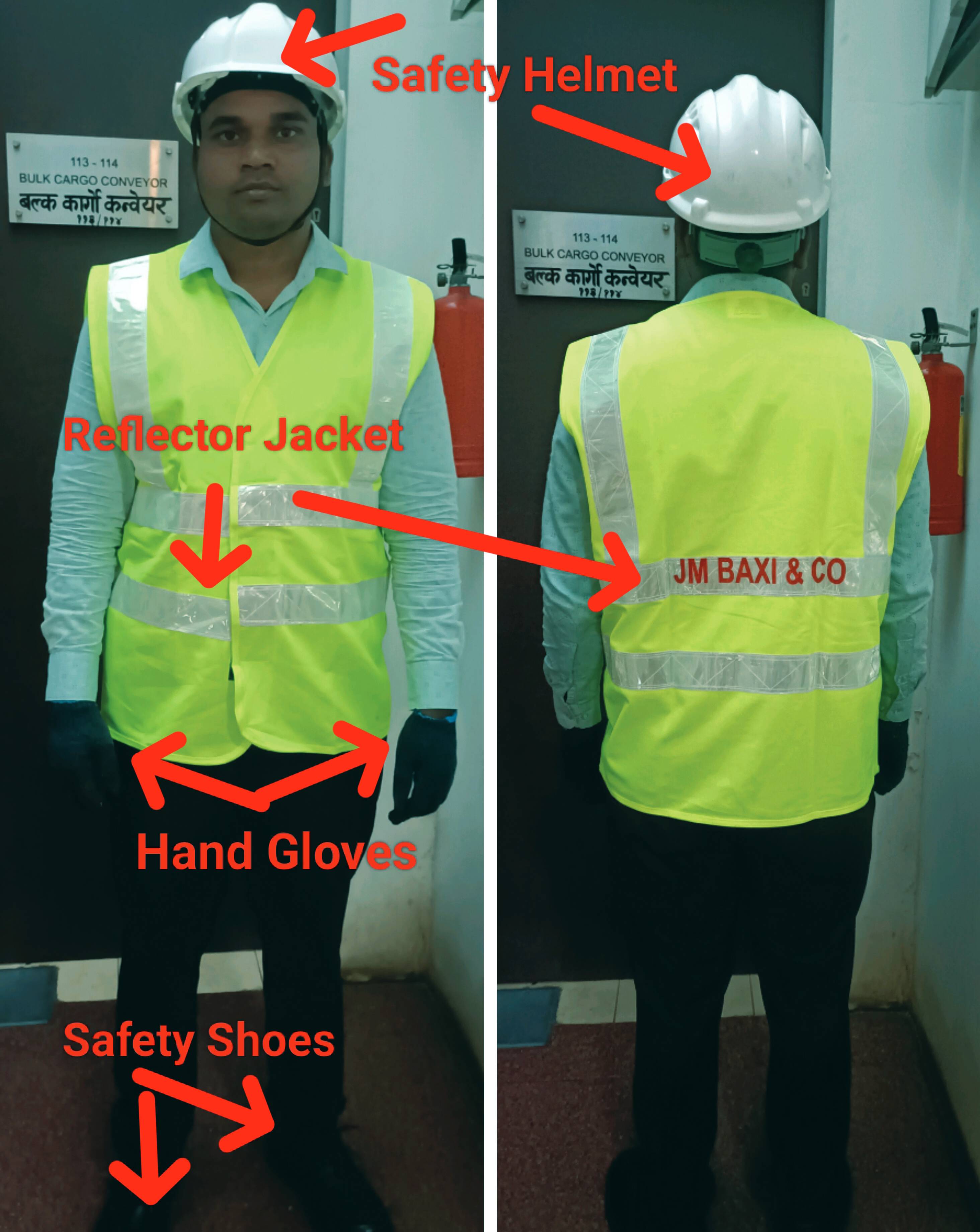
II. Safety aboard vessels
Vessels due to variations in design, condition and the general arrangement of cargo, can present the potential for personal injury and damage. Before working onboard, all workers should assess the layout, set-up and condition of the vessel including access to all Points of Work (POW), no-go-area on the vessel, location of the fire-fighting appliances and all swing zones of all lifting equipment. The range and severity of risks present on individual vessels can vary due to factors such as age, the condition and type of vessel, access to areas of work, condition of lifting equipment, loose gear, the nature and stow of cargo and the vessel's crew.
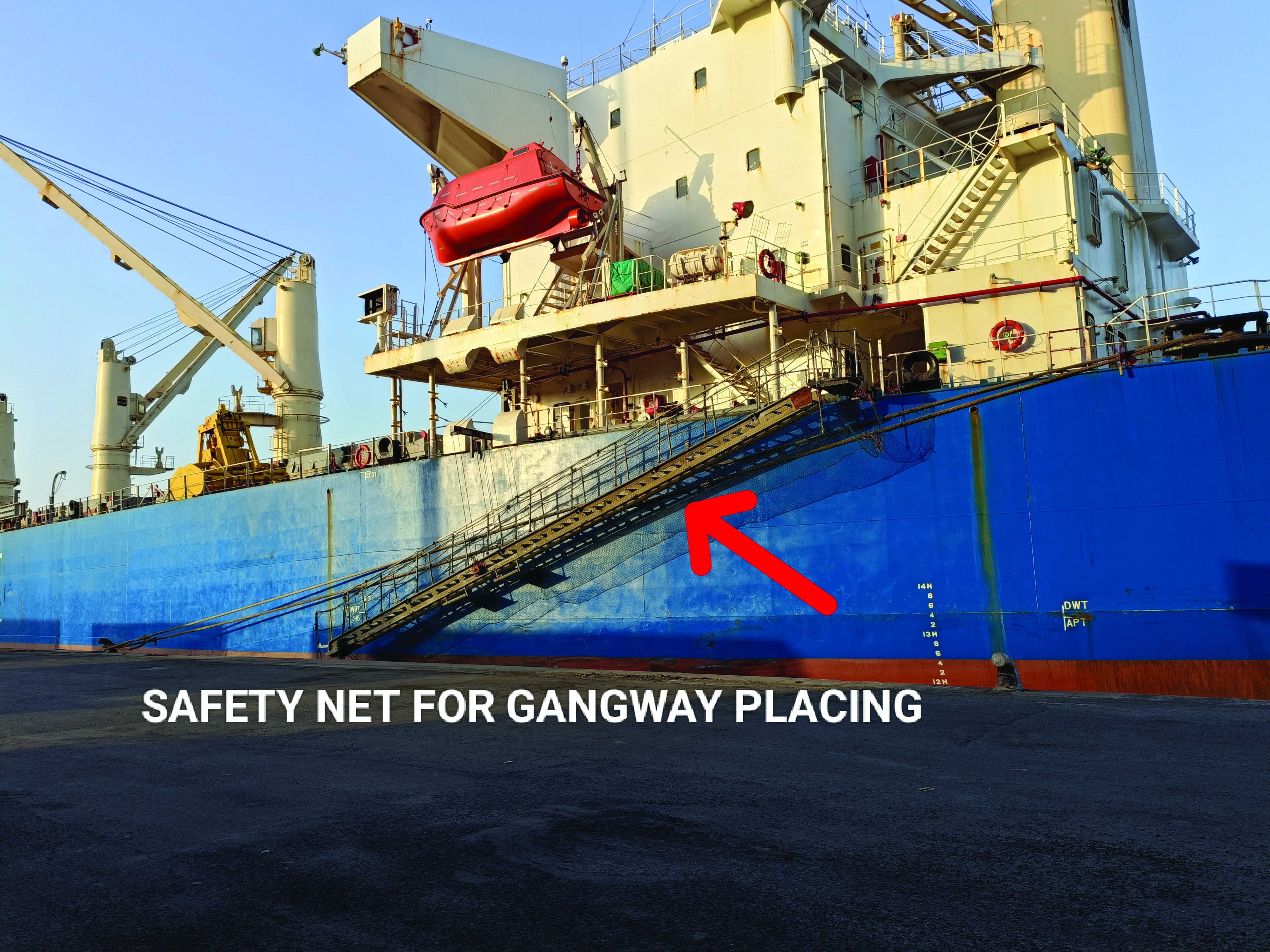
Effective compliance with this standard will be demonstrated by
- Strict implementation of ‘no-go areas’ on the vessel
- Proper head count of the people onboarded, and tallied after the shift when disembarkation from the vessel takes place
- A clear and well-defined line of communication with proper identification of the ship’s officer- in-charge for a particular task; like cargo ops, for maintenance in case of the workshop, for stores in case of supplies etc.
- Ensuring the ship has placed the gangway properly and the safety net is fixed before climbing it
- Cotton gloves must be worn to ensure proper grip while boarding the gangway and checking of steps for any oil or water to avoid slippage
III. Safety from moving equipment
Moving equipment includes light vehicles such as cars, trucks, vans, shuttle buses and other personal vehicles, in addition to reach stackers, cranes, forklifts, trains, etc. used in operational areas. The supervisor and employee should identify and control the risks associated with the usage of moving equipment.
Effective compliance with this standard can be demonstrated by
- Following traffic management protocols and avoiding areas cordoned off by the port
- Operators undergoing competency-based safety trainings
- Safe operation of vehicles and moving equipment
- Managing operator fatigue
- Ensuring only required workers are present within the working area and others are moved out from the area
- Adequate identification and management of hazards and risks
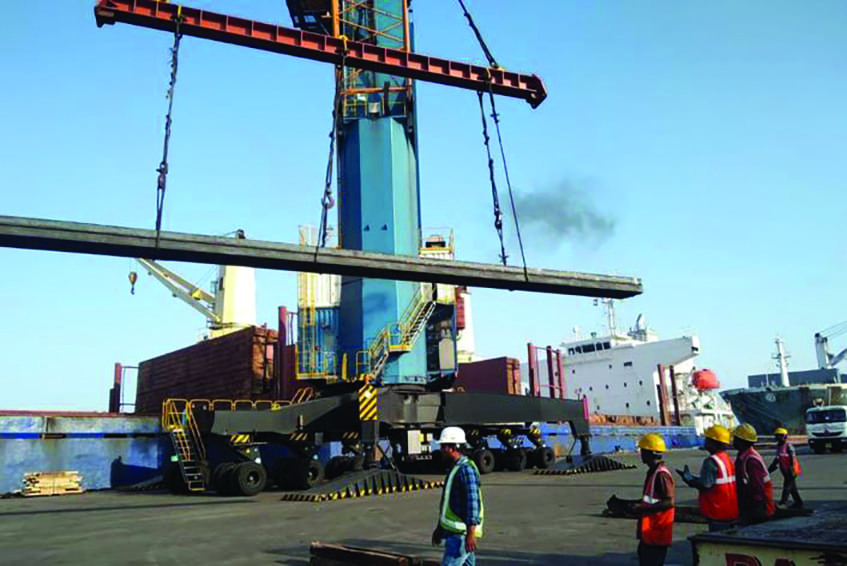
IV. Cargo handling
Many incidents, sometimes fatal, are reported whilst workers are standing under the cargo load or the impact zone in cases of falling loads. Supervisors are advised to use the appropriate equipment and safe work procedures to eliminate the likelihood of personnel being injured by swinging, shifting or falling cargo loads during cargo handling operations.
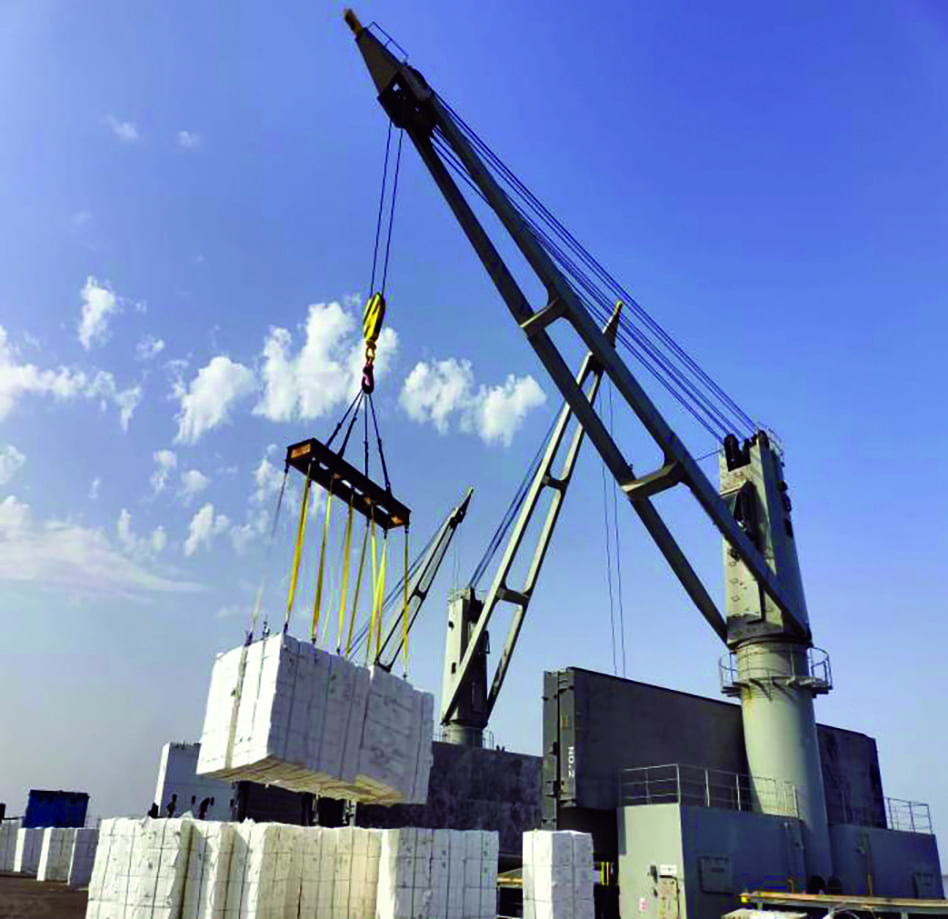
Effective compliance with this standard can be demonstrated by
- The appointment of a person in-charge of cargo handling operations
- The selection and correct use of appropriate lifting gear and attachments to handle cargos
- The safe operation of cranes and other equipment, including the ship's gear and lifting devices
- The use of safe-load slinging techniques and slinging configurations which result in the minimisation of cargo swing
- Effective communication between all people working in and around a lift
- Ensuring that vehicles are not permitted to enter or leave the site unless cargos are adequately secured
V. Safety when working at heights
Working at a height poses significant risks, even a simple task like climbing the crane ladder, working from the hatch coamings can be fatal due to the location of the working area. Supervisors should ensure employees and workers are safeguarded against the risks associated, whilst working at a height by putting appropriate safety measures like safety harnesses, use of cherry pickers etc. Strict compliance is to be made with all local statutory requirements whilst working at heights.
Effective compliance with this standard can be demonstrated by
- Minimising the need for work to be done at a height
- Using a safe working system comprising of appropriate fall prevention and protection measures
- Identifying and controlling risks when cargo stowage is challenging
- A proper briefing session before the commencement of such activities and checking of control measures like safety harnesses, working in pairs etc. are in place.
VI. Lifting equipment safety
The supervisor shall provide lifting equipment that is designed, built, procured, and maintained to relevant industry standards, to ensure the safety of its personnel and the efficiency of its operations is maintained. Lifting equipment covers all the machinery, lifting tools, lifting appliances, and includes equipment such as cranes, access equipment, lifts and hoists, pressure vessels, general machinery, spreaders and scaffoldings.
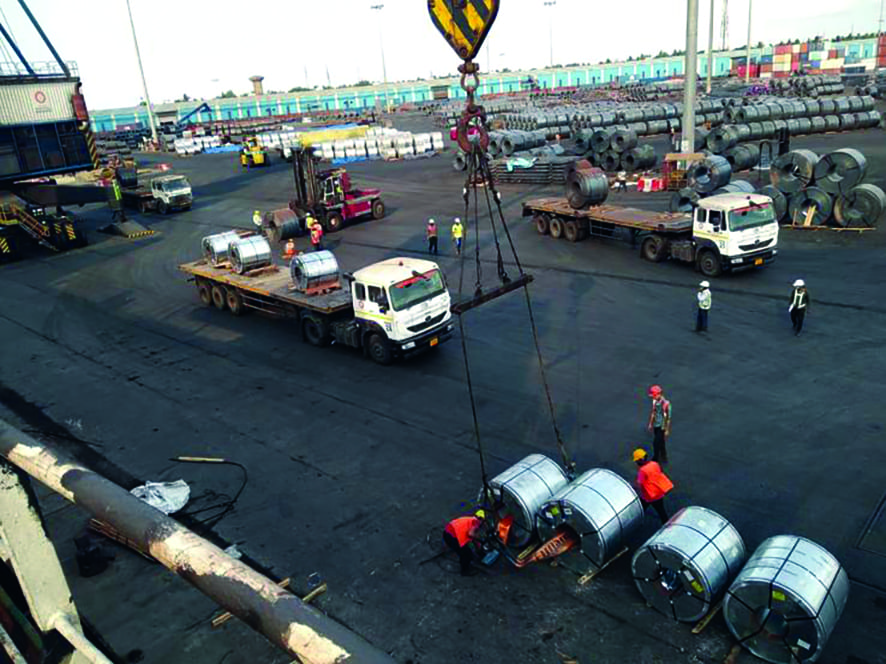
Effective compliance with this standard can be demonstrated by
- A proper maintenance procedure and schedule should be complied with for all the lifting equipment used for operations. Greasing of moving parts of a crane, inspection of wires and slings, periodic load tests of the equipment and slings etc.
- Proper labelling and markings of the swing circle, safe working load, testing dates on the lifting equipment
- Appropriate use of lifting equipment for the kind of operations.
- Spreaders for long loads, wire rope protectors for sharp-edged loads, etc.
- When purchasing new lifting equipment, consideration should also be given to the impact on the environment and the health and safety of personnel operating, working with and maintaining the lifting equipment
Safety is continual and an everyday target. Therefore, safety processes need to be constantly evaluated and evolved to ensure everyone reaches home safely every day. As they say, ‘you live – you learn’.
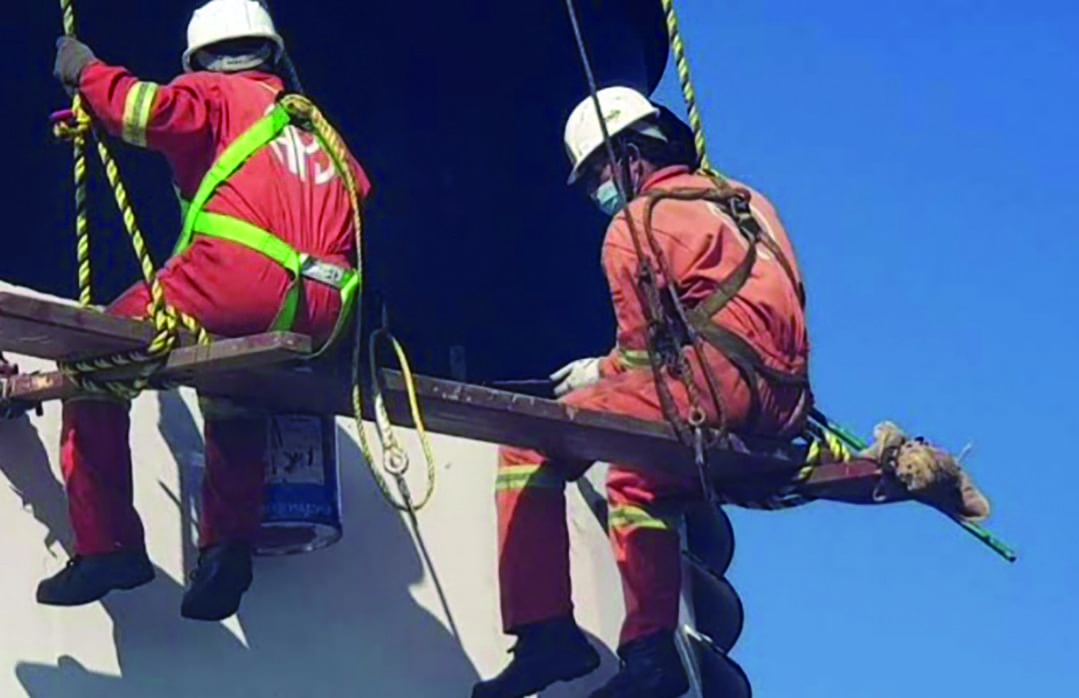