The onset of the COVID-19 in 2020 brought the entire shipping industry to a standstill. The sudden worldwide disruption impacted the global supply chain, throwing trade out of gear. While the world is now becoming accustomed to dealing with the pandemic, the rollercoaster of challenges remains, characterized by a shortfall of vessels, container shortages and increasing freight rates.
- SHORING THE PROBLEM
Considering the fact that the current container demand levels are here for the long term, there are yet no signs of tapering off. Thus, cargoes would continue to be 'decontainerized' into breakbulk modes and the trade explores to charter Multi-Purpose Vessels when they can find them, to meet their container obligations.
When countries began to accept that COVID-19 was a worldwide challenge, consumer demand slumped, leading shipping lines to cancel many of their routes between Asia and North America. This left ships mid-way between consignment pick-ups and deliveries, leading to a chaotic buildup of containers in places where they were not supposed to be. To make matters worse in March of 2021, a 20,000 TEU container vessel, Ever Given, ran aground in the Suez Canal. The six day blockage, further effected the circulation of containers and exacerbated the shortage. Additionally, to tide over the crisis of container shortages and the volatile freight regimes, traders gradually started exploring shipments in break bulk mode instead of the existing containerised shipments. Break bulk cargo is transported in bags or boxes and takes less space in ships, thereby allowing more cargo to be transported, aiding faster exports. Various commerce departments started seeking information from the industry on the type of packaging being used for their cargo and shipment weight, to finalise the list of goods that can be exported as break bulk cargo. The idea was to create a database of all commodities that can be exported via priority berthing as break bulk cargo in order to facilitate faster export of suitable commodities.
The container shipping sector continues to push cargo to breakbulk and Multi-Purpose Vessels (MPV) carriers as distressed shippers and their forwarders cope with port congestion, skyrocketing container rates, and severe equipment shortages.
Today, even more cargo is transported in jumbo bags, which are made in many sizes, for contents usually between 500 and 3,000 KG. The outer layers of such bags are woven with polypropylene for strength and an inner layer of polyethylene. Transportation is usually done by lifting the bags from their loops. These bags come with one, two or four loops at the top, depending on whether they are to be lifted by, crane or forklift. For easy handling by forklifts, the bags may also be transported on pallets. The jumbo bags are filled from the top, and some are arranged so they can be emptied from the bottom or are just cut open, if not re-usable. They are usually very handy for transportation of cargo in powder, pellet or granulated form, but may also be used for nodule types of products, like potatoes, onions etc. A lot of raw materials for the chemical industry are transported in jumbo bags, and they are commonly used for products like cement, fertiliser, salt etc. Jumbo bags are gaining popularity so fast that there are now international conferences for producers and users.
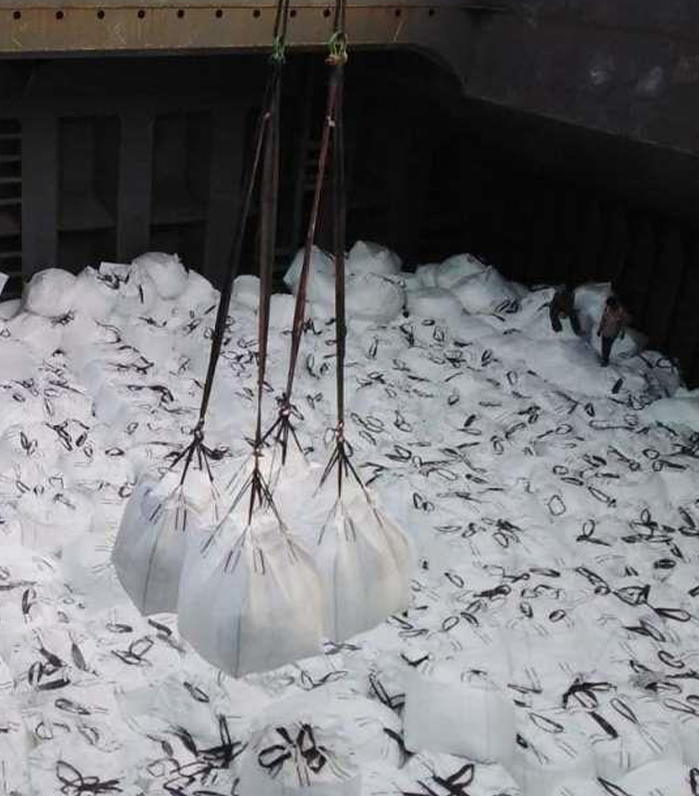
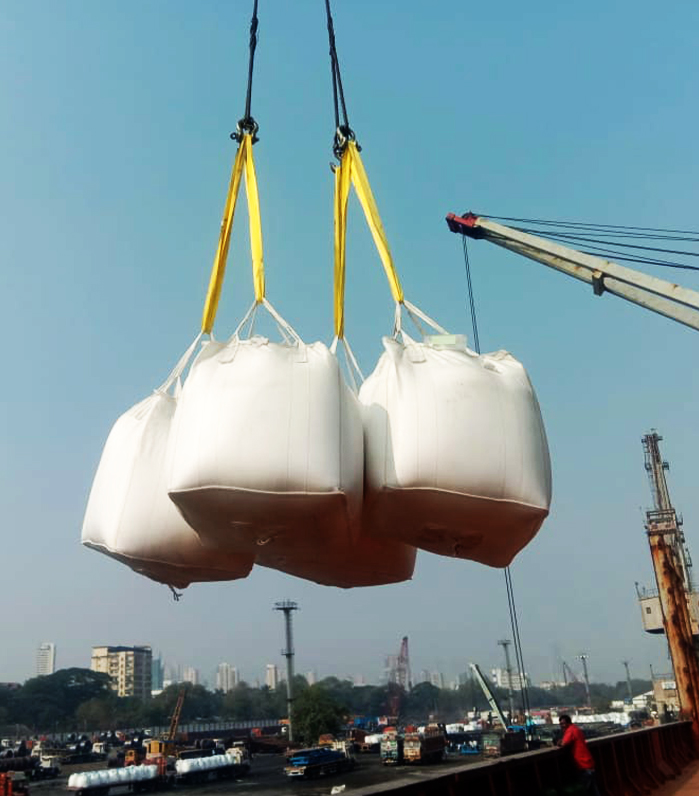
The import of bagged cargo especially Purified Terephthalic Acid (PTA) is majorly taking place around the West Coast of India. J M B axi as shipping agents have been proactively involved with the imports and are servicing clients with ship agency activity along with stevedoring. The cargo is being loaded from the Far East Ports of China, Taiwan and Thailand which are subsequently discharged at the ports of Dahej, Hazira, Nhava Sheva (JNPT) and Mumbai. In less than a year J M B axi has handled 0.2 MMT of PTA at these ports.
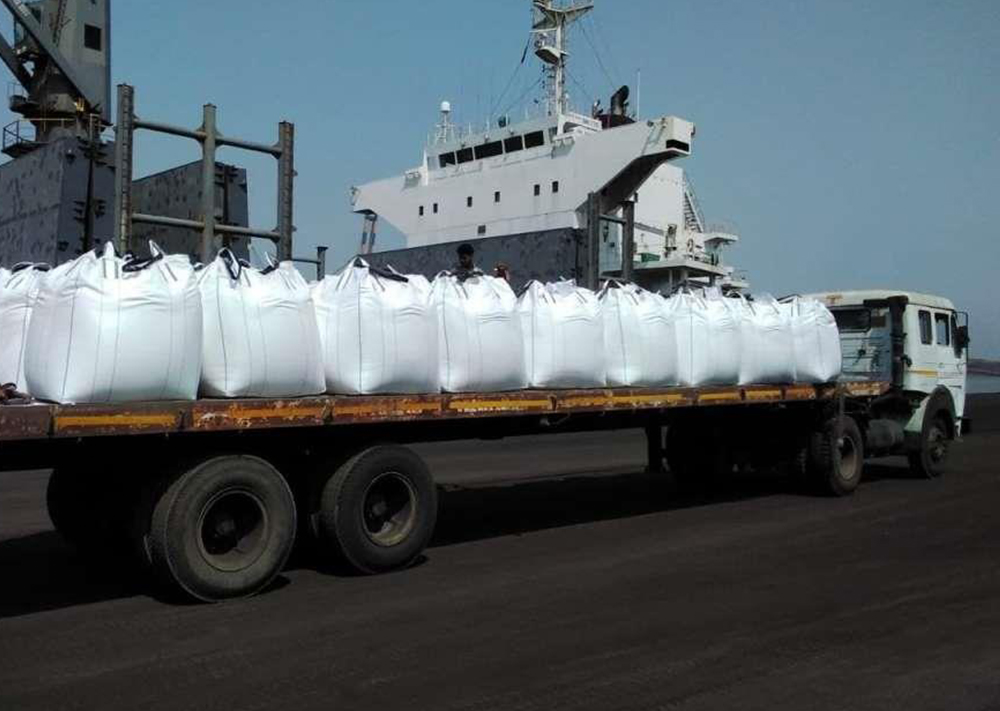
The De-Containerization process is finding its way in the reefer business too. Charterers are seeking substitute options to use conventional reefer vessels for cargo movement. They are fixing cargo/commodities that have not been fixed in breakbulk for over a decade, from places like Chile, South Korea, Japan, Norway and Brazil. Even though reefer fleets are small, with more tonne miles and a surge in demand, the engagement of fleet has gone up from an average of 60-70% utilisation to almost fully utilised. This shift has been due to lack of reefer container capacity or congestion/ delays on container services that would result in the loss of product or market opportunity.
The J M B axi group as a shipping support service provider has been in talks with a few charterers to import fruits, in palletised form carried through reefer ships, though the Indian port infrastructure is not sufficiently equipped to handle refrigerated cargoes due to the lack of cold storage arrangements and reefer points inside the port. J M B axi as an alternate arrangement will be providing, multi fold activities under one umbrella and will support the operation with their century old ship agency expertise along with stevedoring. This shall include offloading of palletised fruits from the vessel on to the quay, in cages to avoid damage to the external packaging and engage electrically driven forklifts inside the reefer compartments of the vessel. The pallets upon discharge shall be subsequently stuffed in local reefer containers. The containers thereafter shall be evacuated from the port within the minimum possible time to its own cold storage space, where the pallets will be destuffed and stored till the receivers take on final delivery.
A pilot project is planned to carry 4000 MT of fruits in boxes weighing 18 KGS. These boxes will then be palletised with 49 numbers in each pallet. There will be two such shipments of fruit imports from Brazil and if the industry finds this economically viable this could turn into a new business opportunity.
- VESSEL CONVERSIONS
The industry started contemplating the conversion of bulk carriers to container vessels, as bulkers have sufficient space in the form of cargo holds, which can be utilised for the carriage of containers by exercising due diligence on the stability of the vessel. A container vessel due to the uneven distribution of weight undergoes adverse forces acting on the vessel whilst at sea. Also, the localised weight of the unitised cargo requires the tank tops to be strengthened. The carriage would therefore require erection of cell guides and necessary posting of securing pads. The changeover would have to be done under the strict supervision of the class, which shall ensure that the vessel remains seaworthy post conversion. The ship owners, thereafter, will have to adequately man the vessel and operate it sufficiently to reap benefits of such conversions and adhere to the Carriage of Goods by Sea Act (COGSA) as different jurisdictions may implement different carriage laws mandatorily by statute, which may impose a different standard of seaworthiness.
The cost of conversion and renewed certification has become viable, as the vessels purchased as bulk carrier cost around USD 10 million, and is being converted and sold at around USD 20 million. In spite of adjusting the conversion cost, it can reap a dividend up to 45%. Turkey is amongst the few countries, spearheading this changeover.
- CONCLUSION
The current container demand levels are here for the long term and show no signs of tapering off. Thus, cargoes would continue to be decontainerized into breakbulk modes and the industry will continue to charter Multi-Purpose Vessels when they can find them, to meet their container obligations.