In October 2022, J M Baxi Heavy successfully completed two prestigious projects for Thailand and Singapore. The project commenced in early 2020 when Larsen and Toubro’s (L&T) Modular Fabrication Facility at Hazira and Katupalli were entrusted with projects from Petrofac, an oilfield services company and Linde, a c hemical company. J M Baxi Heavy (then Lift & Shift) was awarded these projects, with the initial engineering works, transport feasibility study, and client approvals, all of which were executed during the COVID-19 lockdowns.
The planning and engineering discussion commenced with studying the transport feasibility. It involved using J M Baxi Heavy’s 3 meter wide, Nicolas axles and a load spreader arrangement that needed to be designed to match the Scheuerle axles awaiting the cargo on the other end in Thailand and Singapore. The movement of the cargo had to also be synced for onward and final delivery to its final destination. Making it even more challenging was all requirements were critical with no scope for change.
Various options were studied and developed by the J M Baxi Heavy engineering teams. After rounds of online meetings to explain the proposed loading drawings, the customer gave the go-ahead for the commencement of developing a detailed engineering roll-out plan.
Thai Oil modules - Petrofac was the EPC contractor for the project and it was decided to explore the transport feasibility of all modules by various means to keep costs within budget, especially given that prices of sea freight had skyrocketed due to the lockdown. Hence a detailed study was conducted for all 99 modules. It was concluded that 26 modules would be transported by road to Hazira Port via axels, and delivered under hook to a Heavy Lift Vessel (HLV). 18 modules were to be transported via barges and split into five voyages to Hazira Port for onward delivery to a H LV. This total of 44 modules were delivered between January and August 2021. The 55 balance modules required special structures to be fabricated, to help lift and transfer the cargoes. It was critical to maintain the stability of the modules on the axles to ensure they do not slip or become unsteady during transportation.
Thai Oil Modules - Petrofac | |||||||
---|---|---|---|---|---|---|---|
Shipment Mode | No. of Voyages | No. of Modules | Wt. Tonnes | FRT | Period | Axle days | SPMT Hrs. |
Road | 4 | 26 | 1,075 | 13,649 | Jan 21 to Oct 22 | 3,276 | 936 |
Barge | 5 | 18 | 1,452 | 22,908 | 121 | 972 | |
RoRo Ship | 9 | 55 | 21,975 | 44,362 | 6,400 | 76,800 | |
Total | 18 | 99 | 24,502 | 80,919 | 9,797 | 78,708 |
While short tide windows, delays due to the monsoons, long detention periods, ship delays etc. were all di regueur, the exception was the expert precision required in the engineering and movement of the modules. T he heavy cargo needed to be lifted off the ground, placed on custom-made stools, loaded on and loaded off the vessels. Some of the modules needed to be loaded, welded and made suitable for sailing, all of which required absolute accuracy at every step of the way.
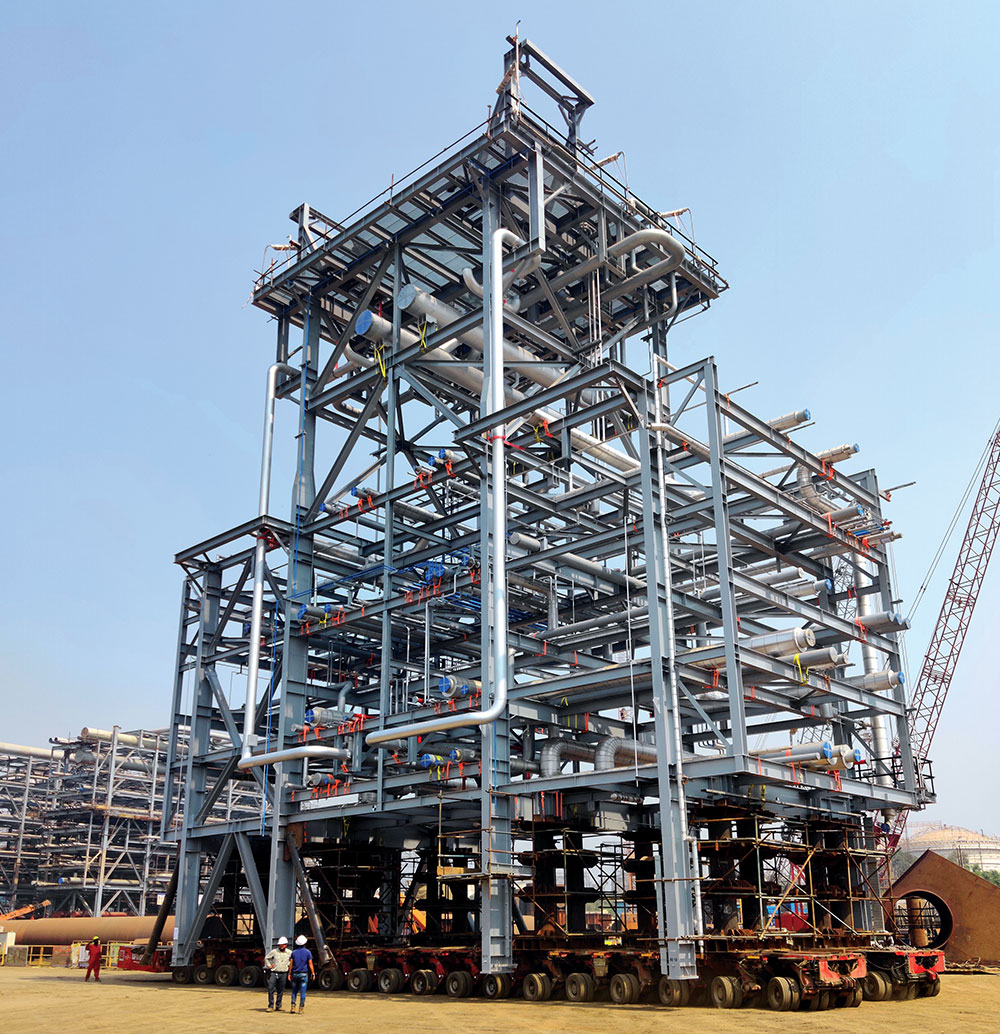
Thai Oil Modules - Petrofac
Singapore Gasification Modules - Linde was the EPC for the project, where a RoRo ship was chartered to transport 46 modules, to be ferried in 10 trips, between March to December 2021. J M Baxi Heavy (then LSPL) had engineered and proposed the loading of modules where for the first time 2 x 3 file axles were positioned as wings and 4 file axles in the centre were combined to transport the heavy modules weighing 2,850 tonnes and 35 min height. The critical engineering elements considered load transfer, the grillage foundation for travel on unstable surfaces, travel within the yard and the roll on to the RoRo vessel.
Thai Oil Modules - Petrofac | |||||||
---|---|---|---|---|---|---|---|
Shipment Mode | No. of Voyages | No. of Modules | Wt. Tonnes | FRT | Period | Axle days | SPMT Hrs. |
RoRo Ship | 10 | 46 | 34,069 | 6,89,567 | April 21 to Oct 22 | 13,408 | 19,956 |
The shipments commenced in March 2021 as per schedule. However post the first two shipments, India faced one of the toughest COVID-19 attacks leading to shortage of oxygen and a stop on all fabrication, bringing all operations to halt and a setback of three months. The shipping delay further complicated issues such as the availability of raw materials. This led to an extended timeline of October 2022, when the last shipment was loaded out.
COVID-19 posed major challenges that required high levels of collaboration over the most minute engineering details. Teams co-ordinated over calls across time-zones and geographies, troubleshooting delays, sudden change in plans, challenges in securing approvals from authorities etc.
Both projects ran parallel, and the teams successfully manoeuvred them with agility and precision, much to the customer's delight.
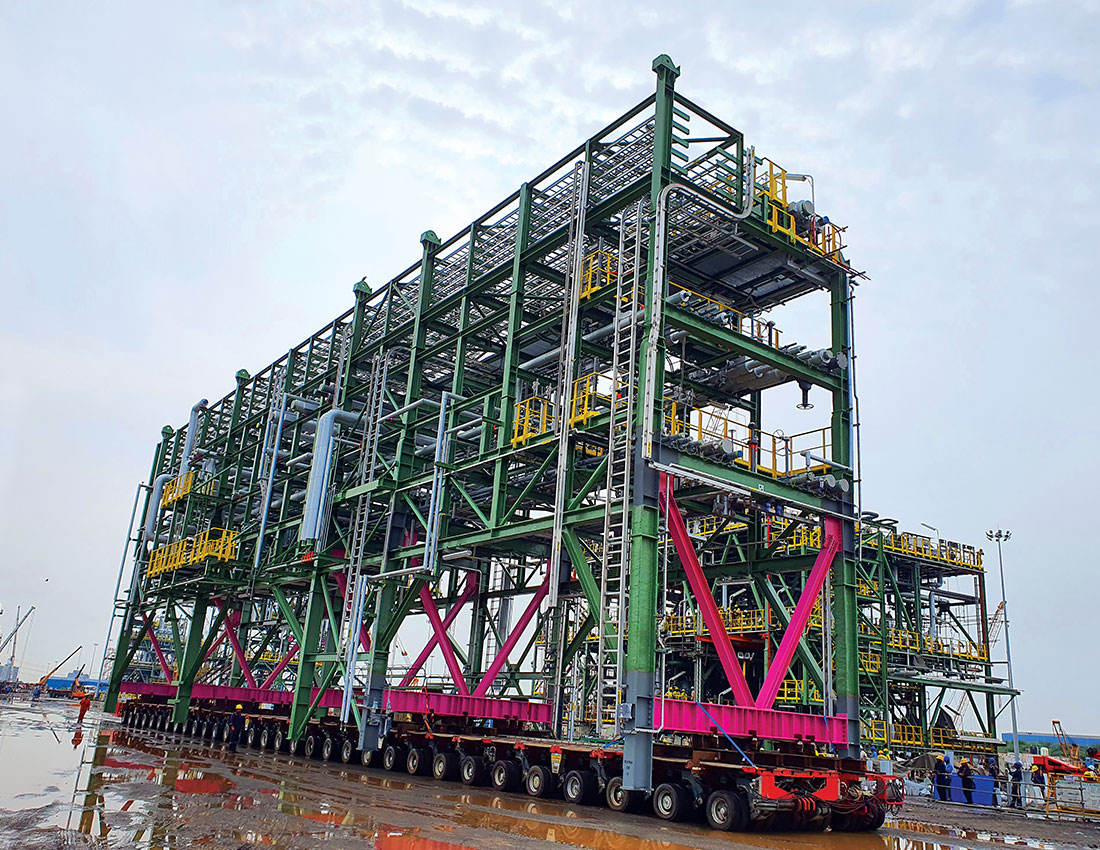
Singapore Gasification Modules - Linde