It was that time of the year when an entire cross-section of the industry was racing to complete their shipments and shift their odd-sized modules from their fabrication yards to the jetty.
These modules were designed and fabricated in partnership with McDermott International Inc., for ONGC’s Vashista project at Kakinada. The job was awarded to Boxco, but it had steep documentation requirements from the various parties involved, i.e., L&T MFF, McDermott and ONGC.
In all, 23 over-dimensional modules were scheduled to be moved according to the barge load-out schedule below.
Sr. No |
Description Of The Module |
Dimensions |
Weight | Qty |
---|---|---|---|---|
1 | Plet 1, 2, 5 & 6 Mudmat |
17.70m x 11.975m x 2.442m |
60.00 MT | 6 |
2 |
In-Line Tee 1, 2, 3, 4, 5 & 6 Mudmat |
16.00m x 12.00m x 2.488 m |
55.77 MT | 6 |
3 |
In-Line Tee 1, 2, 3, 4, 5 & 6 Piping Module Support |
7.75 m x 5.15m x 4.473m |
28.62 MT | 6 |
4 |
Plet 1, 2, 5 & 6 Piping Module Support Framing |
8.25m x 5.15m x 5.032m |
27.87 MT | 4 |
5 | Plem Mudmat |
18.00m x 14.00m x 2.37m |
59.22 MT | 1 |
6 | Plem Piping Module |
13.63m x 12.94m x 8.77m |
101.16 MT | 1 |
Total |
24 |
In addition, a few essential over- sized packages, such as a 7M-high 135 MT tensioner, a 6M-high pipe rack assembly and portable spool base cabins, were scheduled to be moved within the site.
Thanks to Boxco’s in-house technical team, comprehensive supporting data on the methodology of execution and its safety parameters were stacked up for reference, which helped with efficient preparation. The entire methodology was discussed in detail with the L&T technical team, and the proposed methodology was accepted.
With all the preparations in place, Boxco was faced with a high demand for heavy lifting equipment at the time of execution, which left them with limited choices. Despite this challenging situation, Boxco trusted its technical and heavy lift teams to execute the assignment.
Boxco faced quite a few other challenges, such as the need for the following:
Numerous modifications and changes made to the selected equipment, from the tow bar to the steering rod, to adjust to Boxco’s requirements.
Education for the crew and client regarding the arrangement of a disconnected side-by-side axle configuration, which was used to move 13 modules.
Designs for spreader beams and saddles for L&T to suit Boxco’s transportation model for the remaining 10 modules.
Preparation and updates for documentation and execution basis revised plans.
Alert turn manoeuvring within the site due to the disconnected axle arrangement.
Matched barge schedules to move two to three modules in a single shift.
Boxco’s heavy lift team’s skill set was tested often. However, the earnestness behind the team’s efforts and its due diligence resulted in the completion of the assignment to L&T’s satisfaction.
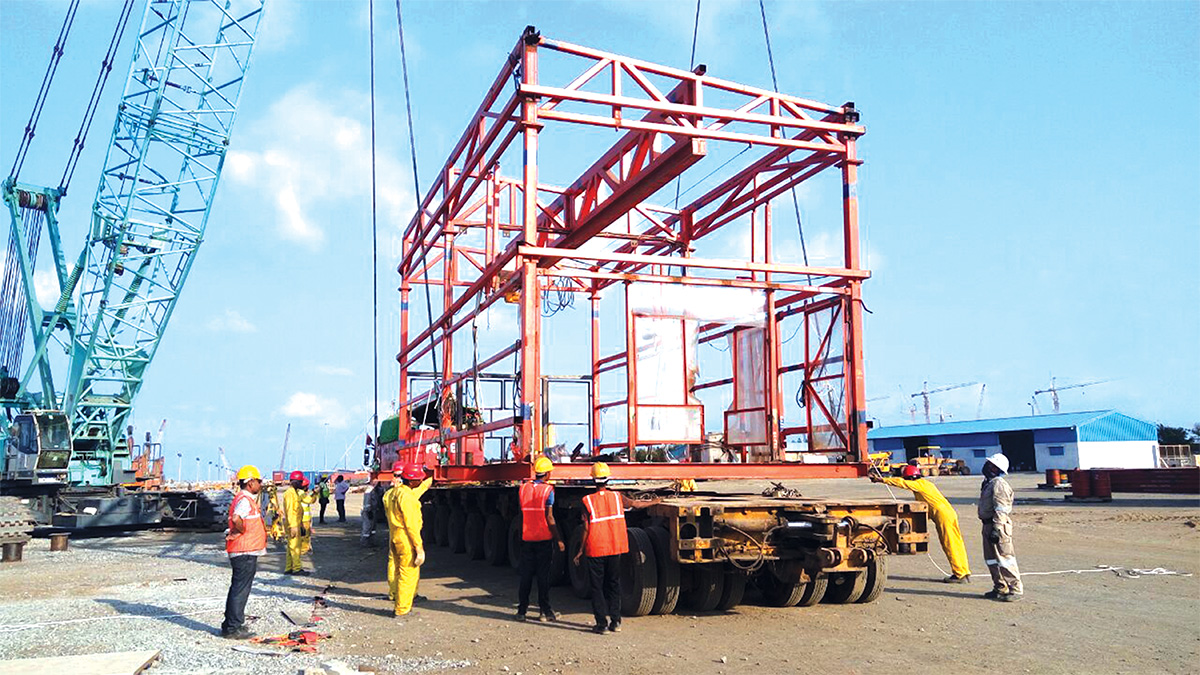
PIPE RACK ASSEMBLY
The team’s combined effort to conquer all the challenges reminds us of the saying “None of us is as smart as all of us.” The L&T team not only conveyed their delight with the timely, safe, seamless completion of the project but also assured us of their continuous support. After earning this priceless experience and valuable reputation, Boxco aims to accomplish more shipments of this nature in the future.
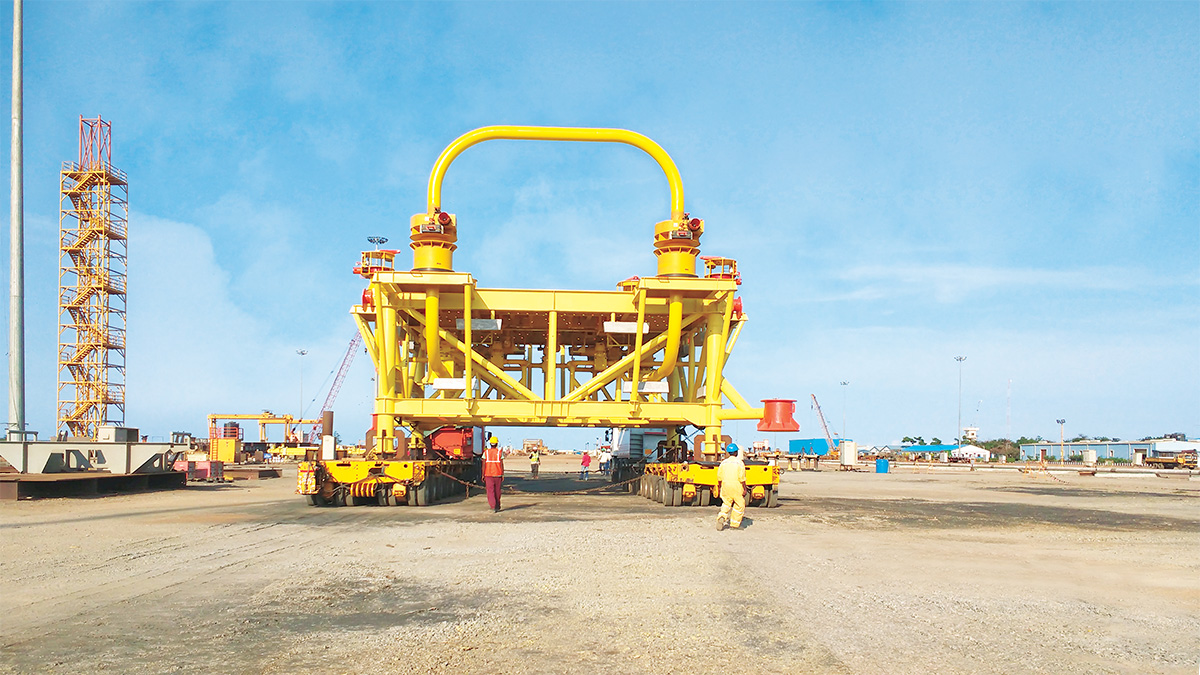
PLET PIPING MODULE SHIFTED BY 2 X 10 AXLES SIDE BY SIDE DISCONNECTED CONFIGURATION
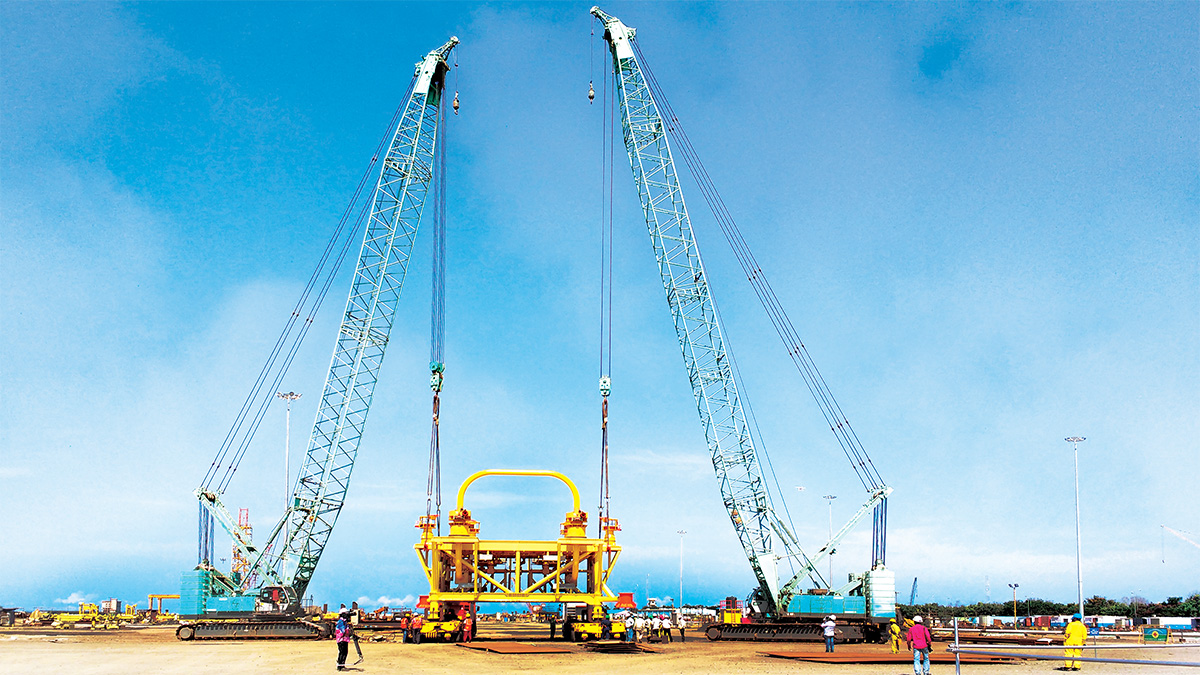
LIFTING VIEW OF PLET PIPING MODULE
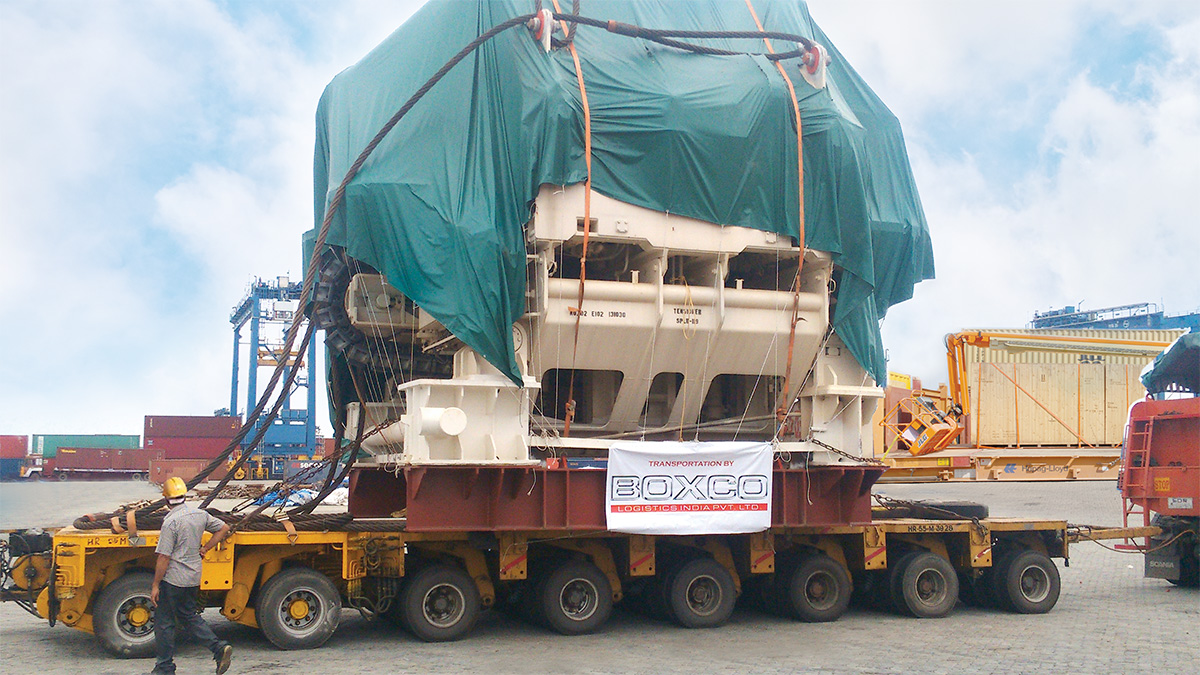
"7M HIGH TENSIONER" PACKAGE IMPORTED AND TRANSPORTED FROM KATTUPALLI PORT TO SITE